Ministry of Science & Technology
New low cost technology reduces textile effluent pollution significantly
Posted On:
22 JUN 2023 7:07PM by PIB Delhi
A textile and apparel industry, located in the Hanumakonda district, of Telangana has been able treat its textile wastewater at a very reasonable cost. Thanks to an energy-efficient and eco-friendly technology developed using, biosurfactants and membrane technology.
Textile effluent is heavily contaminated with pollutants such as dyes, dissolved solids, suspended solids and toxic metals and there is a need for robust, efficient technologies to treat such effluent before they are discharged into the environment.
NIT Warangal along with Prime Textiles, Rampur located in Kakatiya Mega Textile Park (KMTP), with support from IMPRINT, a joint effort of MoE and SERB, developed a pilot-scale textile effluent treatment plant using biosurfactants (BS), cavitation (a process in which pressure variations in a liquid can in a short period of time cause countless small cavities to form and then implode--C), and membrane (M) technology.
Initially, the scientists Prof. Shirish H. Sonawane, NIT Warangal, Dr. Murali Mohan Seepana, NIT Warangal, Dr. Ajey Kumar Patel, NIT Warangal and Dr. Mousumi Debnath, Manipal University Jaipur (MUJ) developed individual systems at the laboratories and the process parameters were optimized. The biosurfactant to be used in Moving Bed Biofilm Reactor (MBBR) was extracted from microorganisms isolated from textile effluent and textile effluent contaminated soil by MUJ.
The use of BS in MBBR helped in dye removal and was effective in reducing operational time and cost (with respect to other biological treatment methods). Cavitation (C), an advanced oxidation process (AOP), aided in reducing installation cost as well as reducing carbon footprint.
The ability of the technology to generate oxidizing radicals in-situ, significantly reduced the reliance on external oxidizing agents. On the other hand, modifying the membrane (M) surface using boehmite sol synthesized using sol-gel process, decreased the pore size from micro-scale to nano-scale and led to a significant improvement in its performance. After optimizing individual systems, a pilot-scale setup has been set up at the Prime Textiles premises.
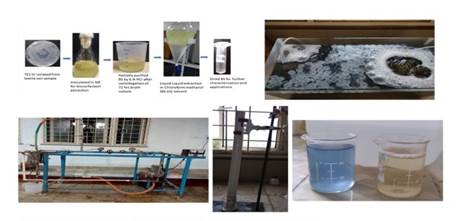
Figure 1 Laboratory developments of the MBBR, HC, and CM systems
The sequence of events that takes place in the pilot plant plays an important role in the treatment process of the effluent. The coagulation removes turbidity caused by suspended solids by destabilizing the charges of the particles using a chemical coagulant. The biofilm grown on MBBR reduces the heavy metal content, degrades the biodegradable pollutants while the cavitation phenomenon destroys all types of pollutants, resulting in the in situ generation of radicals, and energy which are responsible for the pollutant degradation. Finally, surface modified membrane separates all the pollutants present in the wastewater. With this sequence, the pilot plant of 200 Litres Per Day capacity removes pollutants and the treated water can be utilized for agricultural activities, and cleaning purposes.
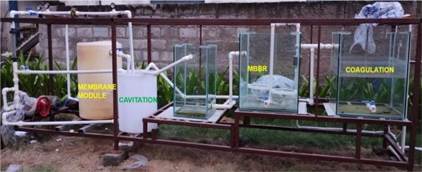
Figure 2 Pilot-scale setup installed at Prime Textiles, Rampur
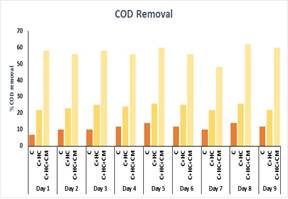
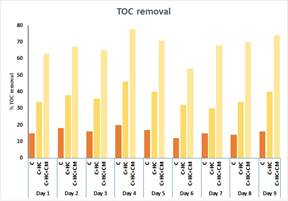
Figure 3 COD and TOC removal using pilot-scale setup
This joint effort has led to the transfer of technology and two patents. The technology offers a sustainable solution for the textile effluent from KMTP, converting the toxic wastewater to irrigation source for the nearby agricultural areas and holds immense potential for replacing existing secondary treatment plants due to its lower installation cost and lesser carbon footprint.
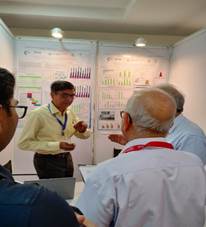
Figure 4 Our team with SERB Scientist Dr. Harish Kumar at the IMPRINT exhibition at IIT Delhi
*******
SNC/PK
(Release ID: 1934582)
Visitor Counter : 2158